What is Lean Six Sigma?
If you’ve been tasked with improving processes within your business, then you’ve probably heard of Lean Six Sigma. But what exactly is Lean Six Sigma and how can you use it to help you and your organisation?
What is Lean Six Sigma?
Lean Six Sigma is a combination of skills and techniques that drive continuous improvement. When implemented, these techniques optimise the performance of an organisation. Improved performance can lead to an increase in profit margins or even stabilise a failing business.
These skills can be applied to any type of business in any department too, not just manufacturing!
Lean
Put simply, Lean reduces the time it takes to carry out a process.
Firstly, wastes are identified within the process. These are steps/actions that don’t add any value, things that the customer wouldn’t want to pay for.
Eight critical wastes:
- Waiting time – delays waiting for things to happen
- Over processing – doing more than what is needed
- Reject work – doing things again because of poor quality
- Motion waste – too much time searching for things needed to complete the process
- Production waste – making more or doing more than is required
- Inventory waste – overstocking tying up valuable cash
- Transport waste – the movement of the process or part around the organisation and finally
- Underutilised staff – lack of upskilling preventing them from being versatile
A Lean system makes a process flow smoothly. The ideal flow is based on one-piece at a time for maximum optimisation.
The flow is balanced by taking out bottle necks and smoothing each step, so that each stage of the process takes the same amount of time to complete. Each of these stages has a set cycle time. The aim is to make each cycle time the same.
Next, the processes are improved further by pulling the product through the system based on customer demand. Customer demand is often referred to as the takt rate of the product. Knowing what the cycle times and the takt rates are for each process enables you to work out the optimum number of people required to do the job. This is an unbelievably valuable calculation for preventing over manning within an organisation!
Lean environments also use visual management tools to make sure efficiency is achieved. The foundation of lean is to create stability and standardisation across the organisation. This is done by implementing and sustaining good 5S practices in all areas of the business.
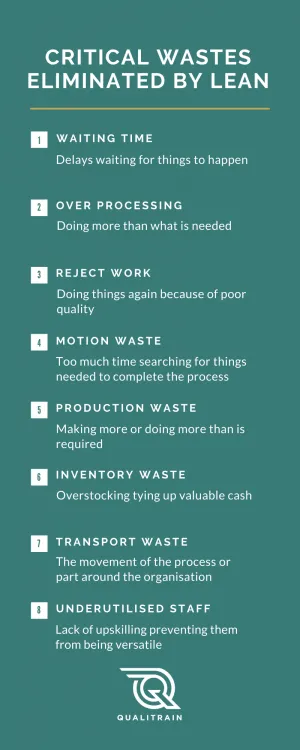
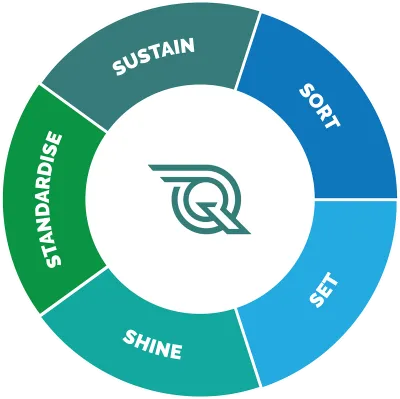
What does 5S stand for?
Sort – clear out things that aren’t needed
Set – put back the things that are needed in optimal positions
Shine – keep the area clean and tidy
Standardise – create standard work and standard operating procedures
Sustain – Audit the area to ensure improvements are maintained.
Standardised practices allow for Continuous Improvement or Kaizen activities to take place. This can only be done once processes have been correctly identified and recorded.
When the Lean foundation has been built this will allow the company to build upon the other Lean working practices to further increase speed through the system, freeing up capacity to take on more work.
Six-Sigma
Six Sigma uses a set of rigorous statistical tools to increase the effectiveness and accuracy of a process.
These tools can be used for measuring and analysing data from the system to identify variation. Firstly, the cause of the variation is identified. Then, the variation is eliminated until the process is consistent. This means products or process outputs can be accurately predicted and ensures zero defects. For an organisation to get to this level of operation, all the lean standardisation practices must be established.
One of the benefits of gathering Six Sigma data is that it allows for fact-based decision making, not relying on your gut! Management decisions can be more accurate, increasing the effectiveness of the organisation.
Like lean, six sigma is driven by the voice of the customer. It is important to understand what the customer requires, and any six sigma activity will identify its impact on them. Why spend months on a project if it is not going to benefit the customer?
Six sigma projects usually follow a DMAIC process. This is an acronym for the five stages of the improvement project:
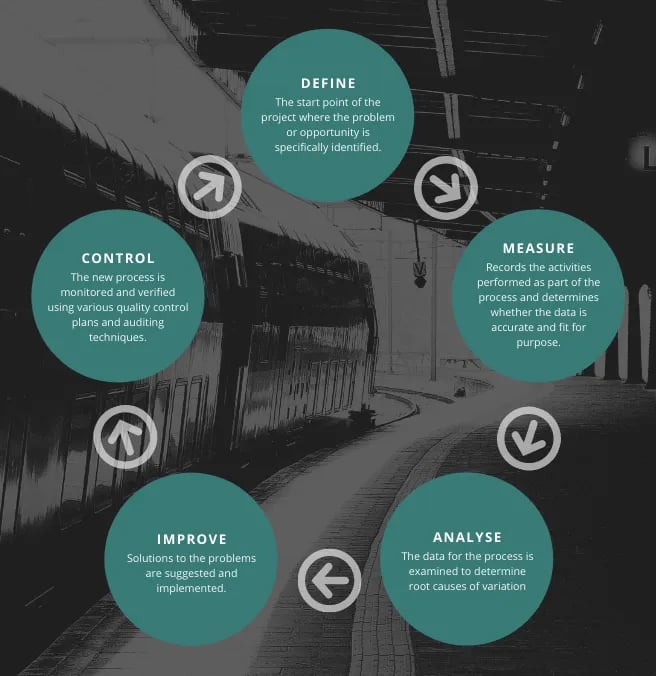
Share this
You May Also Like
These Related Stories
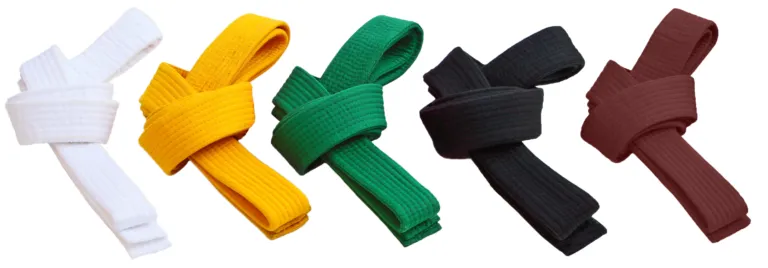
Understanding the Lean Six Sigma Belts
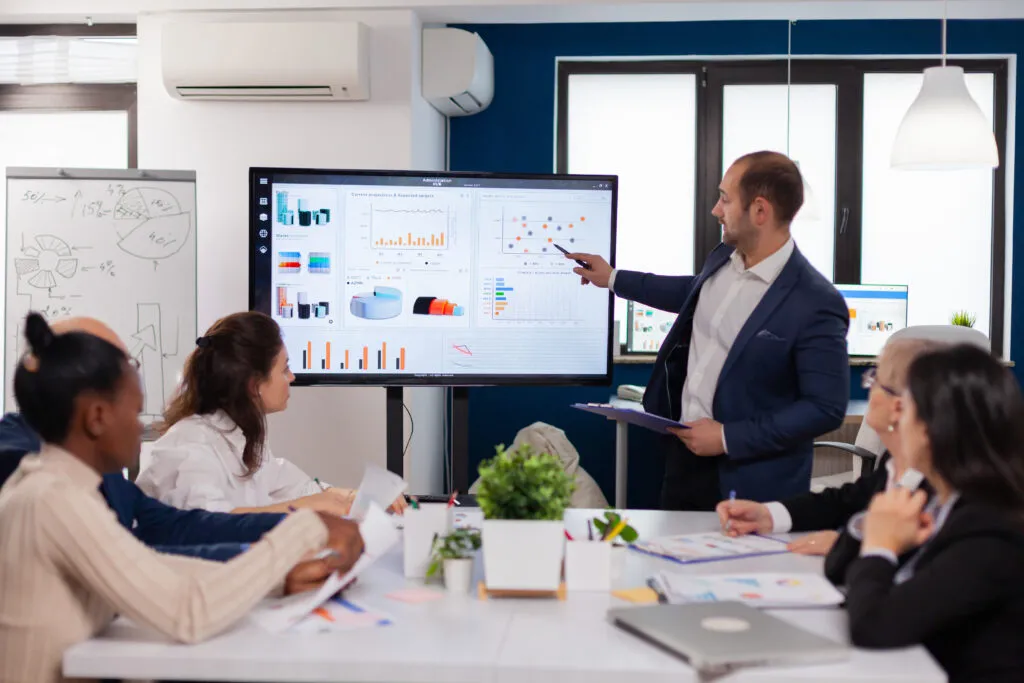
Improvement Leaders drive Continuous Improvements
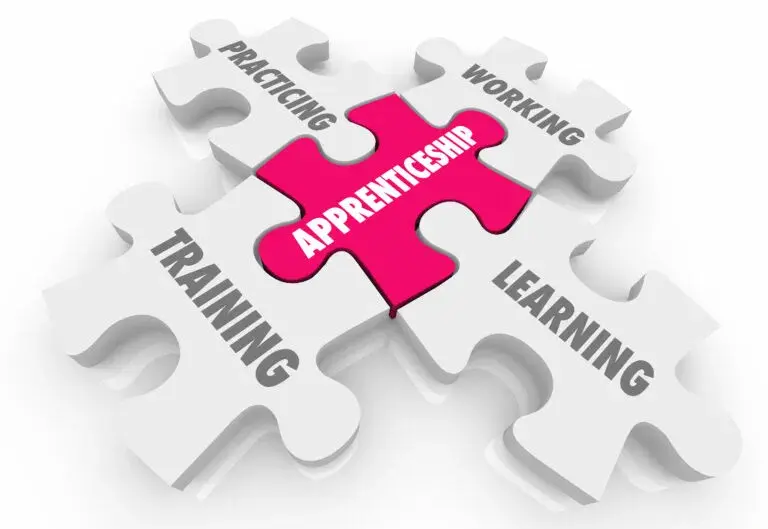
No Comments Yet
Let us know what you think