Level 5 Improvement Specialist
Apprenticeship
(Black Belt)
Leading improvement strategies
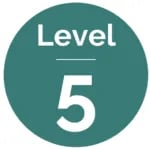
Level 5 Improvement Specialist - Black Belt
Establish specialists to driving improvement
“A leading qualification for Lean Six Sigma in any industrial sector today”
We are a leading, accredited UK Training provider because the experience, knowledge and skills our trainers possess are second-to-none. Between them, our trainers have many years experience in Lean Six Sigma, teaching and training; they provide our learners with an unparalleled support system from enrolment to End Point Assessment.
The role of an Improvement Specialist
Improvement Specialists are responsible for leading the deployment of improvement strategy, for training others and for providing deep technical expertise in advanced Lean and Six Sigma, Project and Change Management principles and tools.
During and after their training, Improvement Specialists will typically report to Improvement Leaders who develop the improvement strategy and governance and provide technical guidance on advanced analysis. The Improvement Specialists manage Improvement Practitioners who lead smaller improvement projects. They will work closely with other Improvement Specialists to support the delivery of improvement strategy, working on multiple simultaneous projects linked to key business objectives.
Find out more about the role and responsibilities of an Improvement Leader in our brochure.
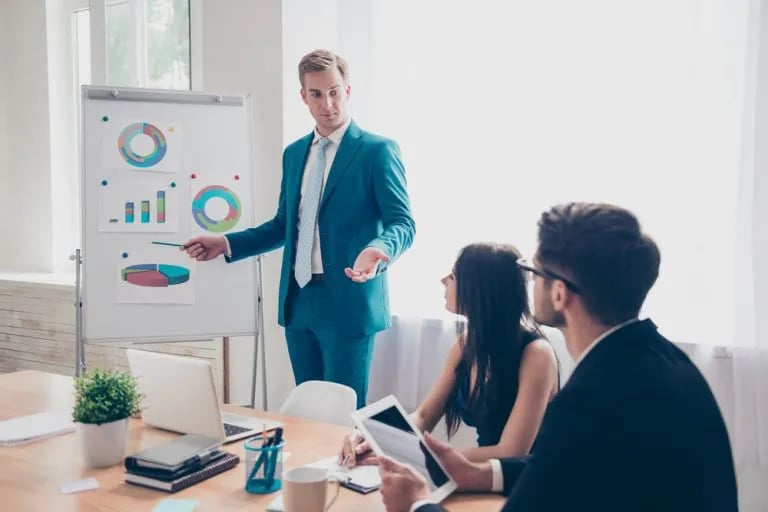
Improvement Specialist Apprentices will learn the following core knowledge and skills throughout their training:
- Leading improvement teams
- Strategic Deployment of Continuous Improvement
- Communication
- Capability Development
- Project planning
- Change planning
- Principles and Methods for Improvement
- Process mapping & analysis
- Lean tools and Measurement
- Statistics & measures
- Data analysis-statistical methods
- Root cause analysis
- Experimentation and optimisation
- Data analysis (Statistical Process Control)
- Benchmarking
- Failure mode avoidance
- Sustainability and control
- Project Selection and Scope
Who is the Qualification for?
Continuous Improvement roles are commonly found in all industry sectors and functions including Automotive, Pharmaceutical, Telecommunication, Retail, Finance, Food, Drink, Travel and Leisure.
What Skills and Knowledge will be acheived?
Leading Improvement teams:
Personality types, team development stages, motivational techniques, situational leadership, learning styles, mentoring models.
Project planning, review & coaching:
Multi-element business case, financial plan, benefits realisation plan, risk management plan, project plan. Maslow’s hierarchy of needs.
Principles & methods for Improvement:
How to apply Improvement Methods across all functions, policy deployment principles, Lean culture.
Statistics & measures:
Probability distributions & how to test for fit of probability distributions to data. Confidence intervals, central limit theorem. Testing data for stability & normality & strategies for dealing with non-stable or non-normal data.
Experimentation:
Principles of full and fractional designed experiments including replicates, repeats, randomisation, blocking & centre points, resolution and confounding.
Failure mode avoidance:
System state flow, boundary diagram, interface analysis tables, fault tree analysis, robustness checklist, tolerance design and analysis. Principles & links between Failure Modes and Effects analysis for concepts, designs, processes.
Sustainability & control:
Control & reaction plans. Prevention controls.
Typically, this apprenticeship will take 14-18 months.
More information about the Core Knowledge, Skills and behaviours, and the entry requirements can be found here.
We also offer the Level 5 Improvement Specialist (Black Belt) as part of our regularly run Open Programmes, which do not require a minimum cohort. Contact us for more information.
At Qualitrain, our accreditations and awards reflect our unwavering commitment to quality, excellence, and industry-leading standards. Each certification and accolade we hold is a testament to the trust our clients place in us and the dedication of our team to delivering exceptional training and support.
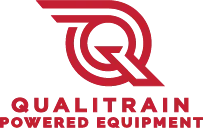
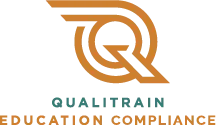
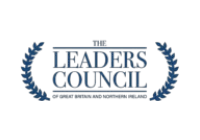

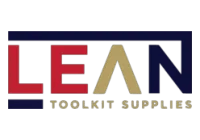
What Our Clients Say About Us
Our Accreditations & Awards
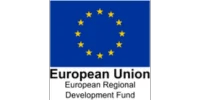
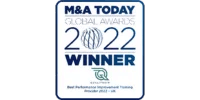
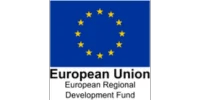
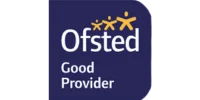
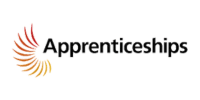
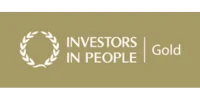
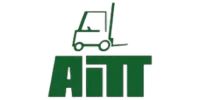
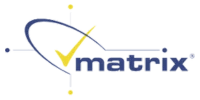
.webp?width=150&height=150&name=IPAF%20Member%20(1).webp)
Our Accreditations & Awards
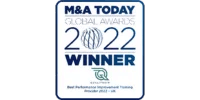
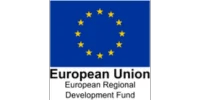
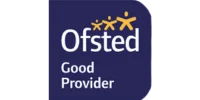
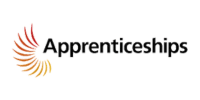
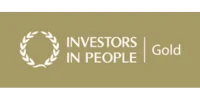
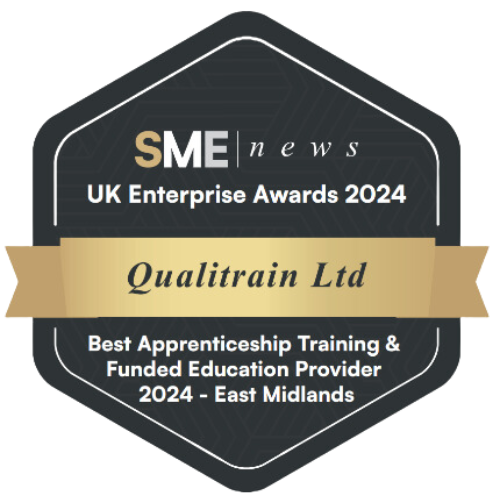
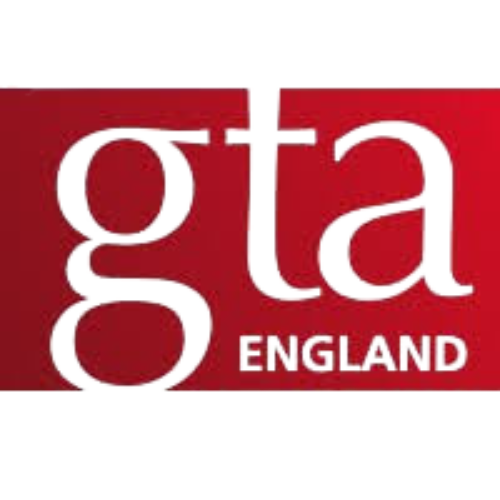
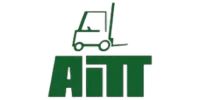
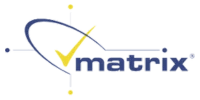
.webp?width=150&height=150&name=IPAF%20Member%20(1).webp)
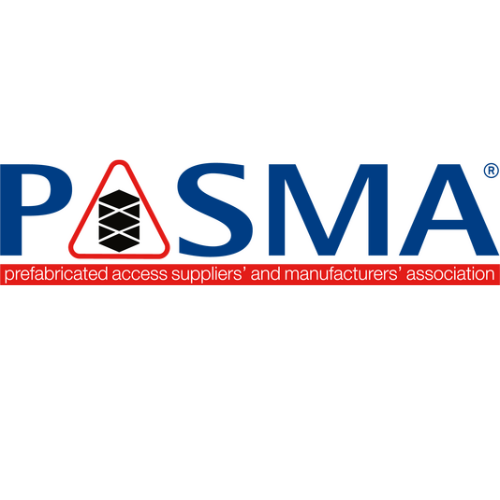
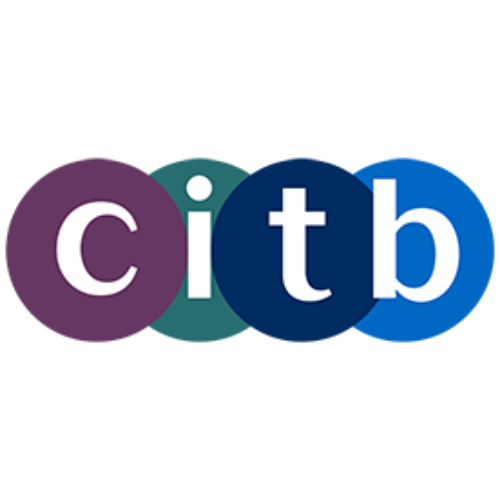
Contact Information
Address: Genesis Centre, 32-46 King Street, Alfreton, Derbyshire, DE55 7DQ
Phone Number: 01773 417340
Email Address: info@qualitrain.co.uk
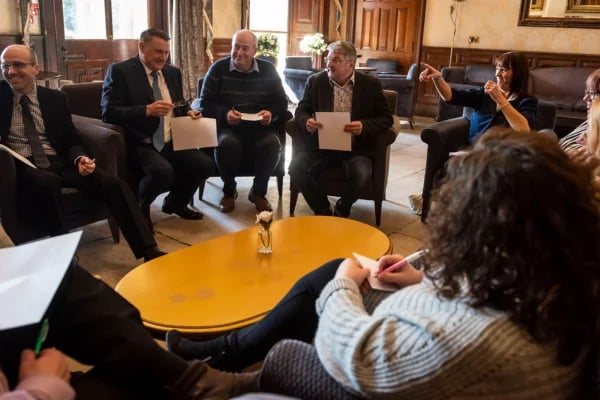
Get In Touch With Us!
From Our Blog
Stay up to date with what is new in our industry, learn more about the upcoming products and events.
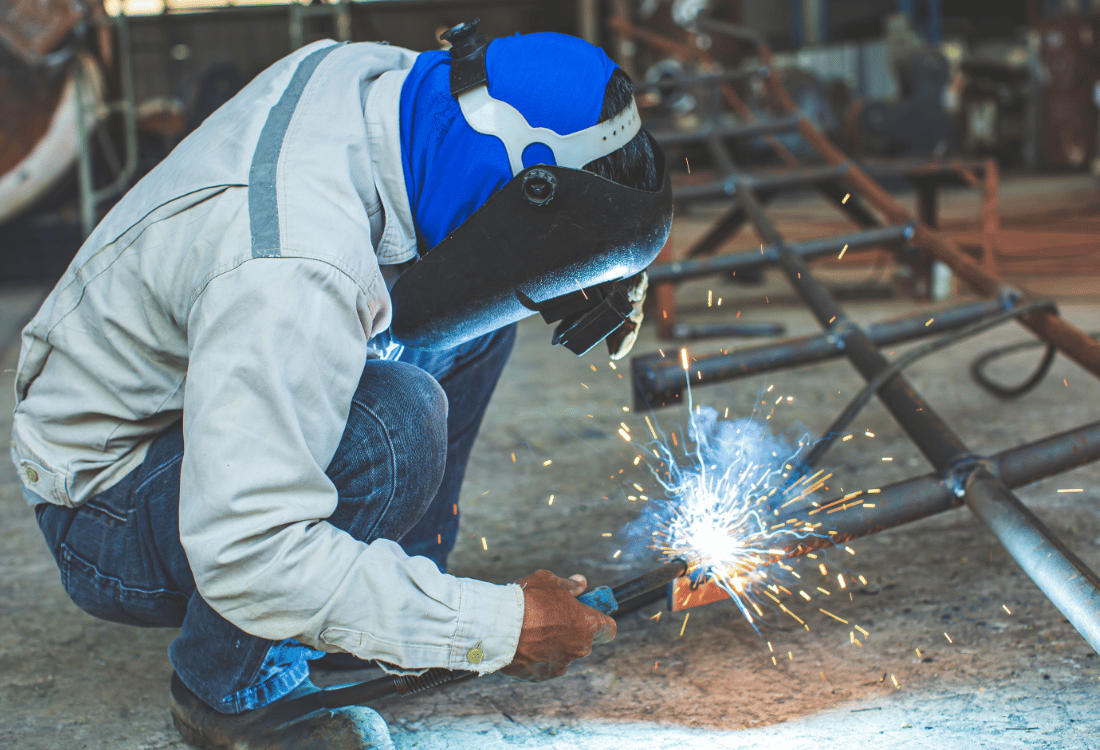
Upskill Your Career Path: A Level 3 Metal Fabrication Apprenticeship
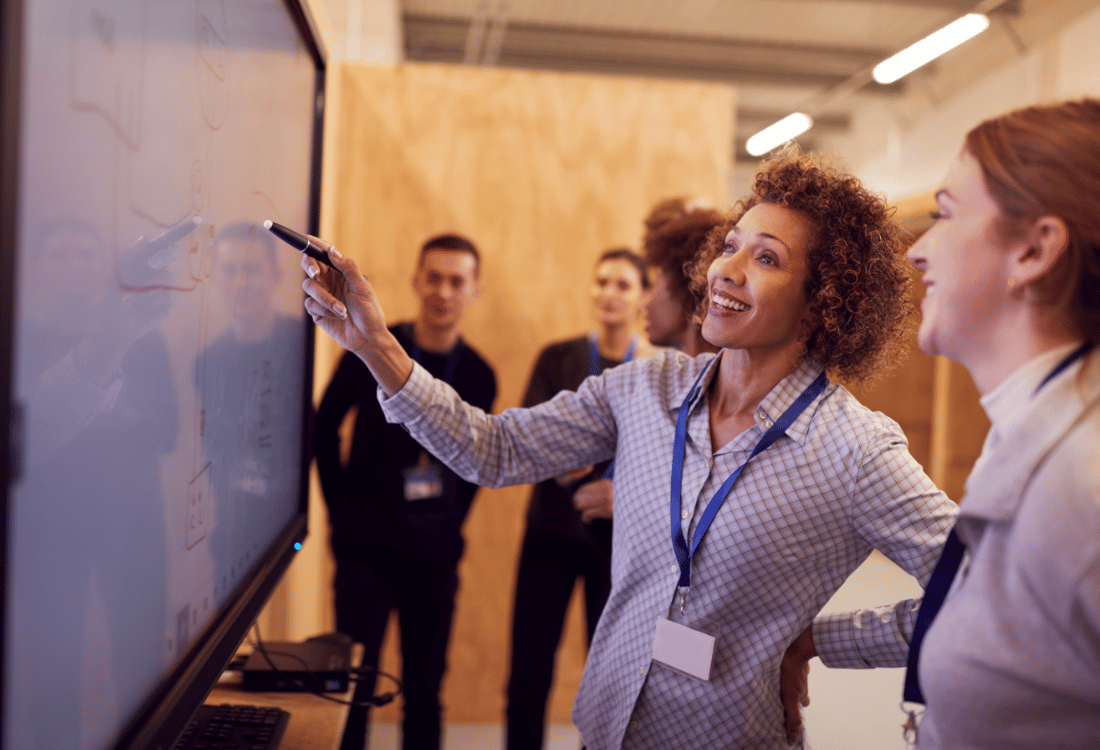
Apprenticeships & Functional Skills Reform: Will There Be Real Change?
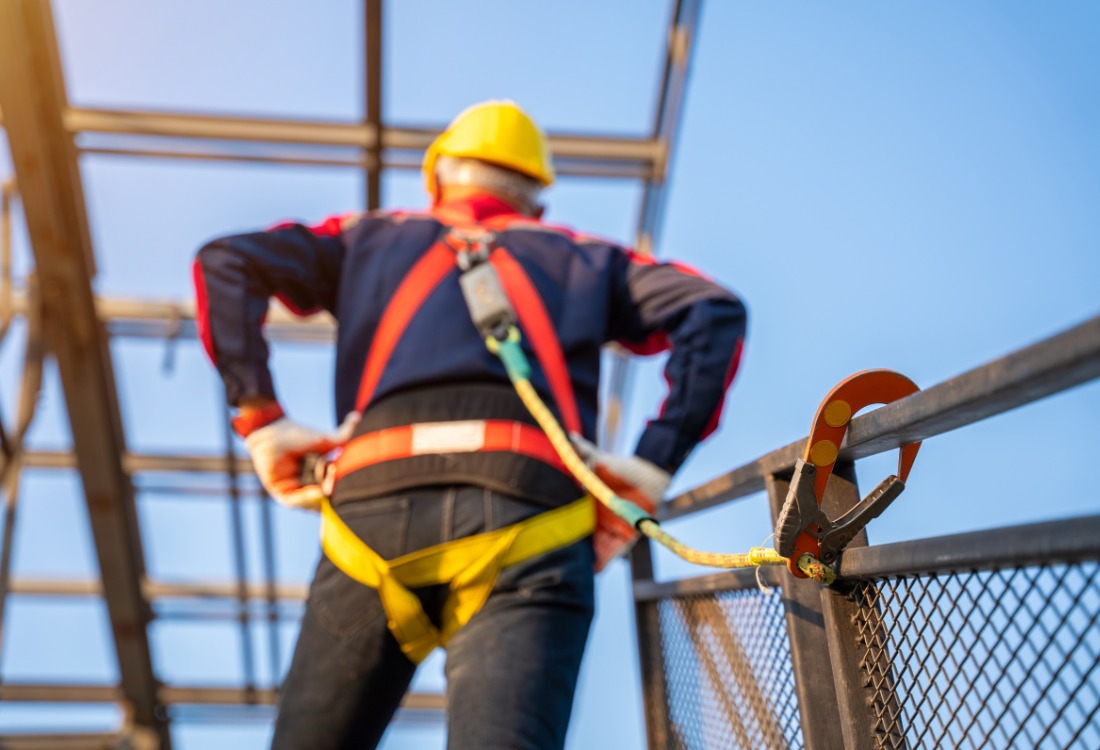